transformer is the most important electrical machine used to transfer electrical energy from one circuit to another without changing its frequency. It is used either to step up or step down the voltage to minimize transmission losses in the electrical circuits. It works on the principle of electromagnetic induction.Since it is a static eectrical device so due to the absence of rotating parts, it has very high efficiency (The basic parts of transformer are its core, primary and secondary windings. Apart from these, there are many different types of equipment installed in transformers that are also considered as parts of transformer, such as its cooling arrangements, protection relay ( Buchholz relay ), HT and LT terminals and bushings, breather, conservator, oil tank, explosion vent, tap changer, etc. So let’s discuss all these different parts of transformer and their functions in detail.
Parts of transformer and their functions
Following are the various parts of transformer:
- Laminated core
- Windings
- Insulating material
- Tank
- Terminals and bushings
- Transformer oil
- Tap changer
- Buchholz relay
- Oil conservator
- Breather
- Radiator and fan
From all the above listed parts of transformer, laminated soft iron core, windings, and insulating material are the basic parts of transformer. These three are available in all types of transformers. Whereas rest of all these parts of transformer can be seen generally in power transformer of rating more than 100 kVA. So let's discuss each part of transformer one by one in detail and their functions.
Laminated core
Laminated core is the most important parts of transformer, used to support the windings of transformer. It is made up of laminated soft iron material to reduce eddy current loss and hysteresis loss. Nowadays in the core of transformer laminated sheets are used to minimize eddy current losses and CRGO steel material is used to minimize hysteresis losses. The composition of core material depends on the voltage, current, and frequency of supply to the transformer.
The diameter of transformer core becomes directly proportional to copper losses and inversely proportional to iron losses or core losses.
Laminated core also provides a low reluctance path for the magnetic flux that minimize leakage flux and maximize the strength of main working flux for transformer.
Windings
In a transformer always two sets of windings are placed on laminated core and these are insulated from each other. Winding consists of several no of turns of copper conductors that is bundled together and connected in series.
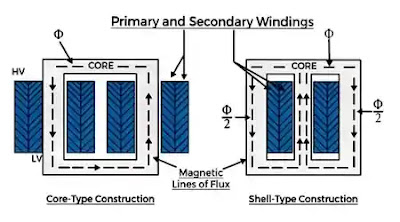 |
windings of transformer |
The main function of windings is to carry current and produce working magnetic flux and induce mutual EMF for transformer action.
Windings are classified in two ways:
- Based on the input and output of supply
- Based on the voltage level of supply
Based on the input and output of the supply, windings are further classified as:
1. Primary winding:- the winding at which the input supply is connected is known as the primary winding.
2. Secondary winding:- the winding from which output is taken to the load is known as the secondary winding.
Whereas based on the voltage level of supply, windings are further classified as:
1. High voltage (HV) winding:- the winding that is connected with higher voltage is known as high voltage winding. It is made up of a thin copper conductor with a large no of turns. It can be either primary or secondary winding of the transformer.
2. Low voltage (HV) winding:- the winding that is connected with lower voltage is known as low voltage winding. It is made up of a thick copper conductor with few no. of turns. It can also be either primary or secondary winding of the transformer.
Hence input and output to the transformer can be connected either on LV-winding or HV-winding as per requirement.
Transformer and all other electrical machines windings are made by good quality copper material due to these properties of copper.
1. Copper is a good conductor of electricity due to its higher conductivity as compared to other materials. So this minimises the power losses in the windings.
2. Other interesting property of copper is it has higher ductility. This means it is very easy to bend conductor into tight winding around the transformer core, that helps in minimizing the amount of copper needed as well as volume and weight of copper.
Insulating material
Since insulation failure can cause the most severe damages to the transformer. So insulation and insulating material should be high grade and it is the most important part of transformer. Insulation is required between each turn of windings, between windings, winding and core, and all current-carrying parts and tank of transformer.
The main function of insulating material is to protect transformer against short circuits by providing insulation to windings so that it does not come in contact with the core and any other conducting material.
Insulating material of transformer should have high dielectric Properties and also good mechanical strength and temperature withstand capability.
Synthetic material, papers, and cotton cloth, etc are used as insulating material in transformer.
Main Tank
Main tank is the robust part of transformer that serves mainly two purposes:
1. It protects core and windings from the external environment and provide housing for them.
2. It is used as a container for transformer oil and provides support for all other external accessories of the transformer.
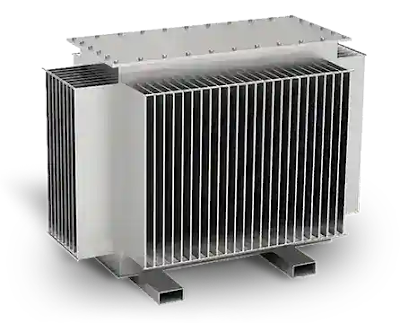 |
The main tank of the transformer |
Tanks are made up of fabricated rolled steel plates. They are provided with lifting hooks and inbuilt cooling tubes. In order to minimize the weight and stray losses, aluminum sheets are also being used instead of Steel plates. However, due to its light weight property, now-a-days aluminum tank is more familiar and costly than a steel tank.
Terminals and bushings
Terminals and bushings are also important parts of the transformer that are used to connecting incoming and outgoing cables of supply and load. These are connected with the ends of the windings conductor.
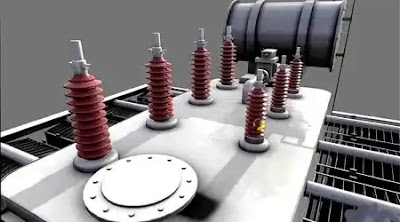 |
bushings of transformer |
Bushings are mainly an insulators made up of porcelain or epoxy resins. They are mounted over the tank and forms a barrier between terminals and tank. They provide safe passage for the conductor connecting terminals to the windings.
As windings are of two types and so bushings are also of two types as named below:
1. High-voltage bushing
2. Low-voltage bushing
The function of transformer oil is to provide insulation between windings as well as cooling due to its chemical properties and very good dielectric strength.
It dissipates the heat generated by the core and windings of a transformer to the external environment. When the windings of transformer gets heated due to flow of current and losses, the oil cools down the windings by circulating inside the transformer and transfer heat to the external environment through its cooling tubes.
Hydro-carbon mineral oil is used as transformer oil and acts as coolant. It is composed of aromatics, paraffin, naphthenes, and olefins.
Tap changer
The main function of the tap changer is to regulate the output voltage of transformer by changing its turns ratio. There are two types of tap changers.
1. On-load tap changer:- in an on-load tap changer, tapping can be changed without isolating the transformer from the supply. Hence it is capable to operate without interrupting the power supply.
2. Off-load tap changer:- in off-load tap changer, the transformer needs to isolate from supply to change its tapping (turns ratio).
An automatic tap changer is also available.
Buchholz relay
Buchholz relay is the most important part of a power transformer rated more than 500kVA. It is a gas-actuated relay mounted on the pipe connecting the main tank and conservator tank.
The function of the Buchholz relay is to protect the transformer from all internal faults such as short circuit fault, inter-turn fault, etc.
When short circuit occurred in winding then it generates enough heat to decompose transformer oil into gases ( hydrogen, carbon monoxide, methane, etc). These gases move towards the conservator tank through a connecting pipe, then due to these gases, Buchholz relay gets activated. It sends signal to trip and alarm circuits and activate it. Then circuit breaker disconnects the transformer from the supply.
Oil conservator
The function of the oil conservator tank is to provide adequate space for expansion and contraction of transformer oil according to the variation in the ambient temperature of transformer oil inside the main tank.
It is a cylindrical drum-type structure installed on the top of the main tank of the transformer. It is connected to the main tank through a pipe and a Buchholz relay mounted on the pipe. A level indicator is also installed on the oil conservator to indicate the quantity of oil inside the conservator tank. It is normally half-filled with transformer oil.
Breather
Breather is a cylindrical container filled with silica gel and directly connected with the conservator tank of the transformer.
The main function of the breather is to supply moisture-free fresh air to the conservator tank during the expansion and contraction of transformer oil. This is because the transformer oil when reacting with moisture can affect the insulation and cause an internal fault in a transformer. That's why the air entering in conservator tank should be moisture free for better life of transformer oil.
In a breather, when air passes through silica gel then moisture present in the air is absorbed by silica gel crystal and hence a moisture-free dry air is supplied to the conservator tank. Thus we can also say that breather is acting as an air filter for the transformer.
Radiator and fans
Since power losses in the transformer are dissipated in the form of heat. So a cooling arrangement is required for the power transformer. Dry-type transformers are generally natural air-cooled. But when we talk about oil-immersed transformers then several cooling methods are used depending upon kVA rating, power losses, and level of cooling required.
Hence to provide proper cooling, radiators and fans are installed on the main tank of the power transformer. Radiators are also called cooling tubes.
The main function of cooling tubes or radiators is to transfer heat generated by core and windings to the environment by circulating heated oil throughout the cooling tubes.
In a large power transformer, forced cooling is achieved with the help of cooling fans fitted on the radiator.